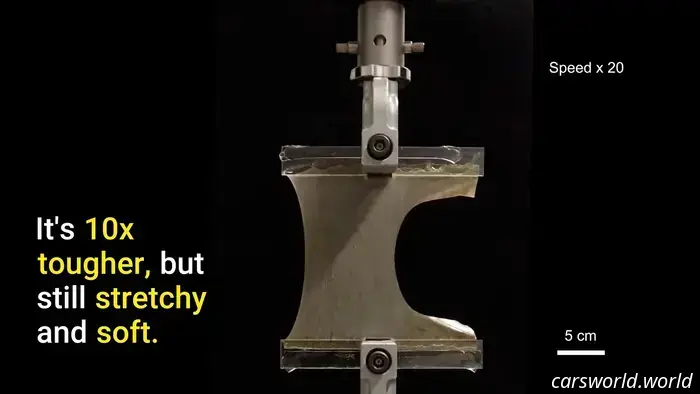
Harvard has developed a method to enhance the toughness of rubber by tenfold, which could have significant implications for the automotive industry.
Harvard School of Engineering and Applied Sciences
Subscribe to The Drive’s daily newsletter
Stay updated with the latest in car news, reviews, and features.
Natural rubber is an extraordinary material. Few inventions have had as significant an impact on manufacturing, and the automotive industry is just one sector that relies on it for essential parts like gaskets, seals, and tires. However, it has a major flaw: it cracks, rendering it nearly useless. This is why researchers at the Harvard School of Engineering and Applied Sciences recently began experimenting with natural rubber to enhance its durability. Remarkably, they managed to make it ten times more resilient by adjusting the vulcanization process.
The science behind the production of vulcanized rubber has remained relatively unchanged since Charles Goodyear patented the process in 1844. It starts with harvesting latex from Hevea trees, which is then coagulated, dried, mixed with additives, shaped, and heated. This intense process creates short polymer chains in the material, leading to the formation of chemical bonds, as noted by Harvard SEAS.
The researchers at Harvard had a novel idea: “What if we treat it more gently?” While it might sound odd, this simple change resulted in surprising outcomes. The modified rubber exhibited four times better resistance to slow crack growth, even after being repeatedly stretched.
“We expected the properties to improve by perhaps two or three times, but they actually improved by one order of magnitude,” said Zheqi Chen, a former SEAS postdoctoral researcher and the paper's primary co-author.
Harvard School of Engineering and Applied Sciences
The revised process was inspired by latex processing techniques and focused on maintaining the long polymer chains rather than creating shorter ones. The resulting long “tanglemers” within the material resemble spaghetti noodles instead of a tightly-knit mesh. This structure allows stress to be distributed more evenly across the tanglemers, significantly enhancing its crack resistance.
In addition to being more crack-resistant, the new material proves to be tougher in conditions that would typically compromise natural rubber. While it may not be entirely accurate to label it as “self-healing,” the stretching of the new rubber and the formation of small cracks enable more crystallization due to the spaghetti-like tanglemers. This leads to an increase in overall strength under such conditions.
This video illustrates it effectively:
This process, however, is not ideal for automotive uses such as tires, at least in its current state. High levels of water evaporation result in a smaller yield of material than manufacturers would prefer for car wheels. According to Harvard SEAS, this innovation is currently better suited for gloves and other thin applications. If researchers can successfully adapt the process for automotive seals, it could bode well for those living in warm climates in the next 10 to 15 years.
Residents of Phoenix are hopeful that this time frame is shortened.
Have a tip or a question for the author? Reach out directly: [email protected]
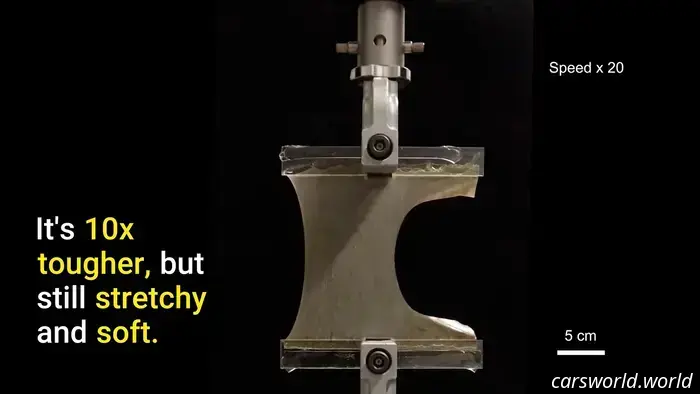
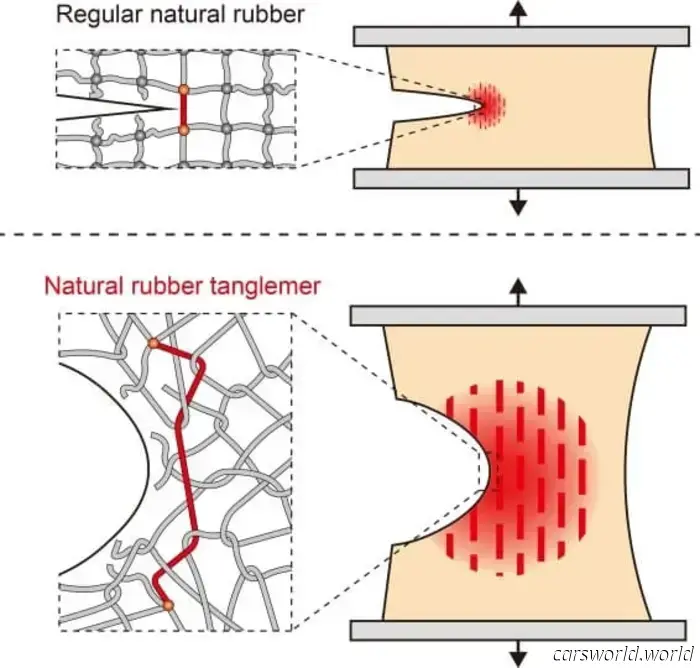
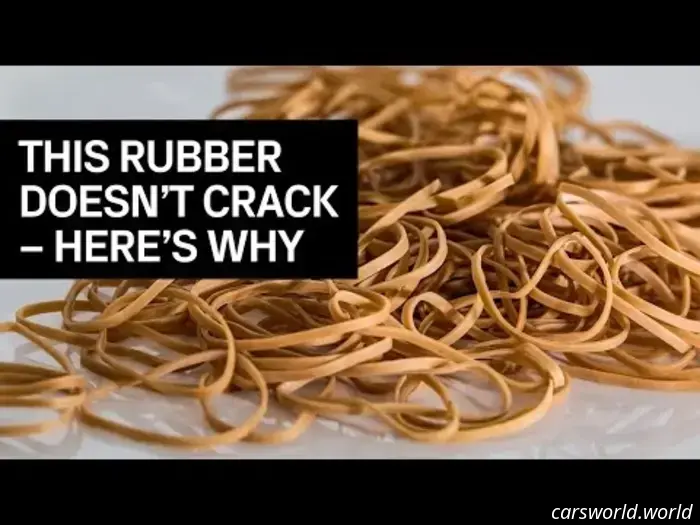
Other articles
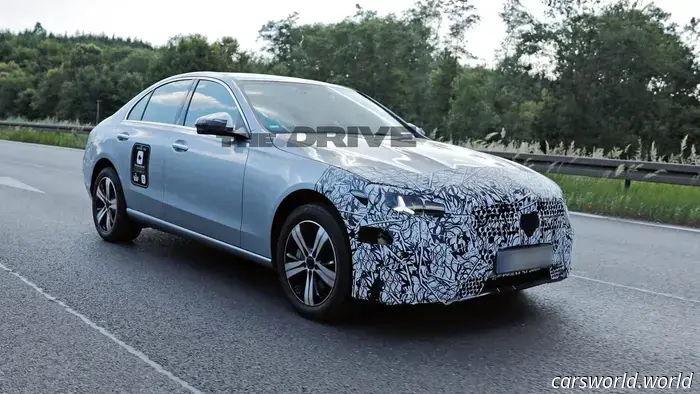


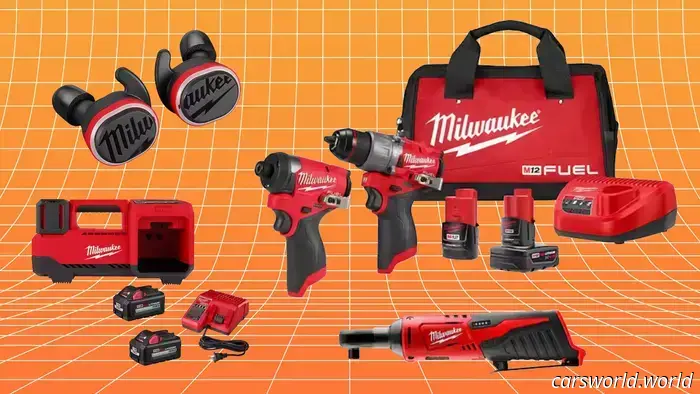


Harvard has developed a method to enhance the toughness of rubber by tenfold, which could have significant implications for the automotive industry.
A modification to the long-established, high-intensity vulcanization method was all it took to create a material that is ten times more durable than standard natural rubber.